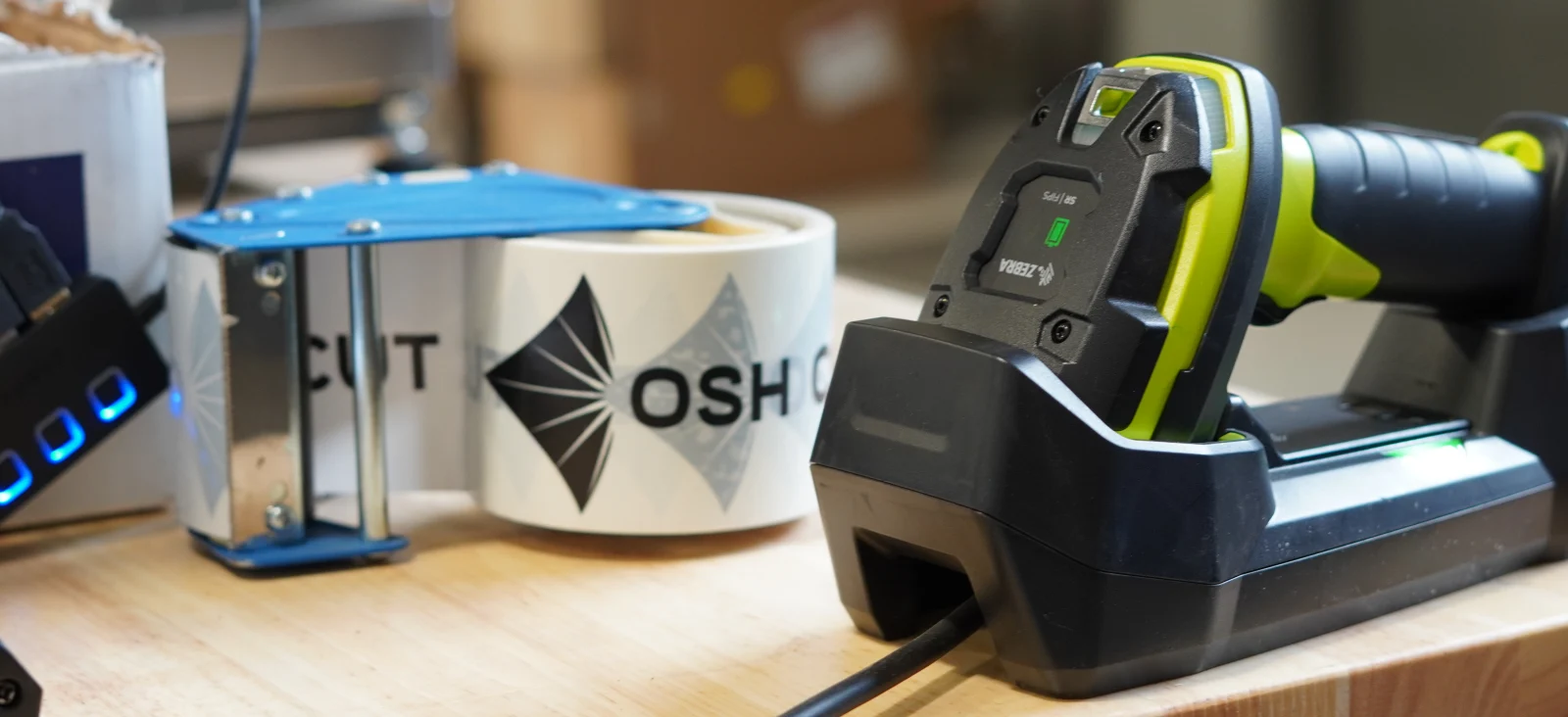
Everything is Changing
In a 1995 interview with Bill Gates, David Letterman famously poked fun at the internet. Responding to a press frenzy about a baseball game broadcast on the internet, Letterman joked, "does radio ring a bell?" and "do tape recorders ring a bell?" Hilariously, Bill Gates struggled to tell a compelling story about what the internet could offer that tape recorders and radios couldn't.
At the time, even Bill Gates didn't really know what was coming. Some 25 years later we can say, "Can you imagine having access to literally a planet's worth of information, in your pocket, anywhere in the world, at any time?"
That's the miraculous world that we live in, and I think that even now we might struggle to understand exactly how massive a technological and societal change that represents. And even more, where this massive digital leap is going to take us.
Exponential Innovation
Rapid innovation is one of the most exciting outcomes of the digital transformation. That applies to every engineered product you can imagine, from cell phones and appliances, to roads and manufacturing processes. An engineer in the 1960s could count on thumbing through books full of printed datasheets days at a time, and producing actual designs was a laborious, manual, time-consuming process.
Having those designs manufactured was equally difficult. You couldn't just get online and upload a 3D model, or even email a print to your local shop. You might have to walk into a shop with a print and sit down with an engineer to discuss it a few hours at a time.
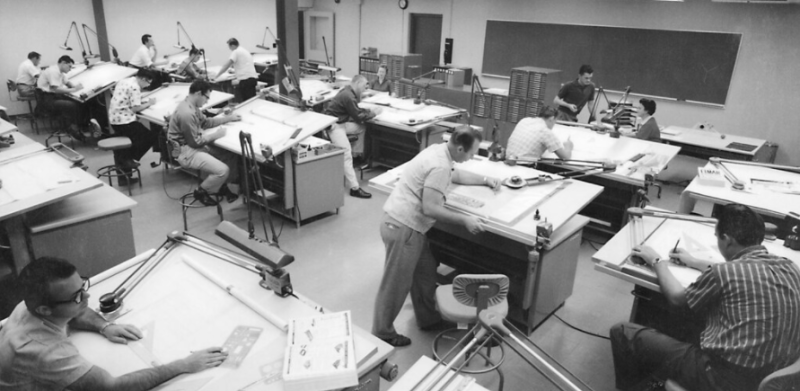
Now, a single engineer with the internet and CAD software might do more than ten engineers in the same amount of time. That means more complex problems can be solved more quickly, products can be developed faster, and the pace of innovation can be again accelerated. New tech enables faster innovation, which spurs development of better technologies and products, which again enables even faster innovation. And so on. It's anyone's guess where this wild ride is going to take us.
Sheet Metal Manufacturing in the Digital Age
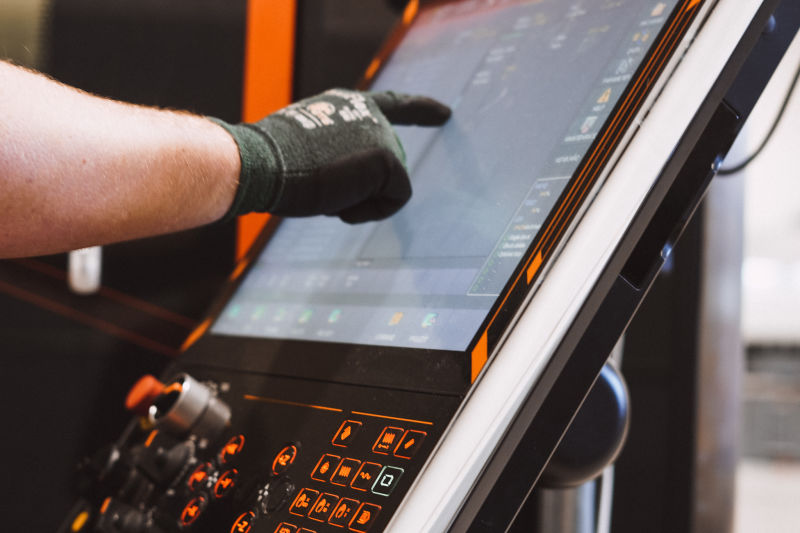
New innovations affect the entire supply chain. Faster engineering means better machines like CNC lasers, finishing equipment, and press brakes. Faster software development means better tools for engineers and designers (eg. CAD software for sheet metal design), better tools for ordering, and (for shops) better systems for managing processes on the shop floor.
Everyone involved in sheet metal production benefits: customers design parts more quickly and easily, shops provide prices and DFM feedback faster, and parts are produced more quickly and reliably than ever before.
We've said before that the sheet metal industry is behind the curve when it comes to technological adoption, but that's not universally true. State of the art sheet metal manufacturing equipment sets new standards for efficiency and productivity every single year. CNC lasers cut metal faster and more precisely than ever before, and they are increasingly reliable and easier to use. CNC press brakes now boast incredible precision, down to automatically measuring material thickness and adapting ram displacement in real-time to make better bends. And programming all this equipment becomes easier and easier, with complex algorithms running under the hood to nest parts efficiently, detect potential issues, and streamline operations.
If the sheet metal world has a problem, it's that ordering and production processes have been slow to modernize. Many shops are still operating the same way they did in the 80s and 90s. Shops commonly receive prints and redraw the parts from scratch in CAD so that they can produce production programs for their equipment. Quoting is almost always performed via email exchange, manually. But all of that is changing.
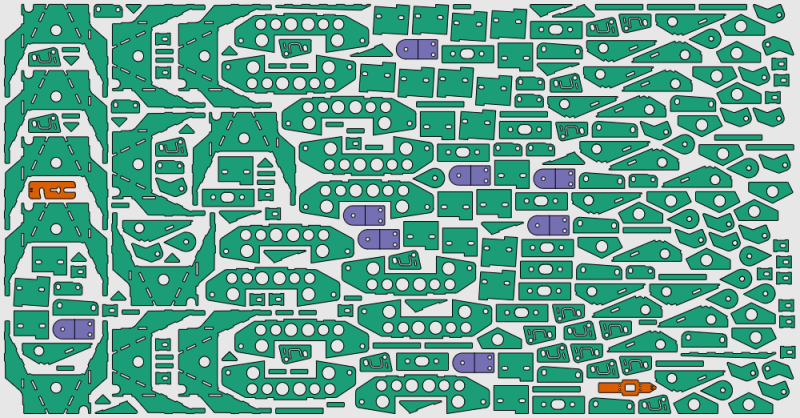
The Shape of Metal to Come
Customer-facing processes in sheet metal manufacturing are being revolutionized, even as we speak. Multiple companies, including OSH Cut, offer fast or instant online quoting on sheet metal parts. And any serious, modern sheet metal company is modernizing its internal software systems to streamline production and reduce waste.
So far, online sheet metal capabilities are somewhat limited. At OSH Cut, we are continuously working to expand the range of services that we offer to make it easier for customers to get what they need. We started by offering blank cutting, then expanded to offer basic air bending using bend lines in uploaded flat patterns. 3D model support with automated unfolding came soon after, as did additional post-processes like deburring and (very soon!!) tapping and hardware insertion.
Within the next decade or two, ordering sheet metal parts with an emailed print will seem as outmoded as designing something on a drafting table. We can't wait to get there.